Bio-Engineering
Hydrophilic Sol-Gel TiO2 Coating on Injector Needle for Development of Procaine-Loaded Injection for Painless Clinical Treatments
Titanium dioxide (TiO2) coatings are demanded in clinical applications due to their biocompatible, porosity, and semiconducting properties. Drug release studies take advantage of these unique aspects of TiO2 for painless injection for those who have to take medicine through the injection frequently. In this study, TiO2 was prepared via the sol-gel method with Titanium tetra isopropoxide (TTIP) precursor in alcohol solvent for pH 3, 4, and 5 values. The prepared solution was coated via dip coating on stainless steel substrates and injectors (Figure 1). Samples were calcinated at various temperatures (100°C, 300°C, 500°C, 700°C). Coated samples' structural, physical, and chemical composition, chemical bond, wettability, and drug-release properties were researched. X-ray diffraction (XRD) analysis showed that at higher temperatures, crystalline peaks appeared, allowing the anatase phase (2θ=25°) which is significant for clinical applications. Contact angle values affirmed that high temperatures and ultraviolet (UV)-light irradiation made samples more hydrophilic (26°±5° at 700°C for pH 4). Drug release studies were carried out by using Franz diffusion cells at 36.5°C. Samples at 500°C calcinated released the highest amount of drug (90 %) for 45 sec injection time (Figure 2).
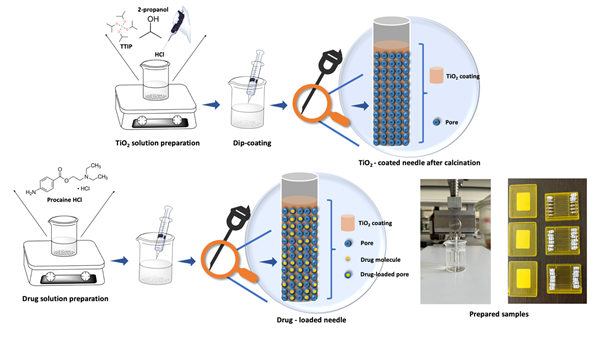
Figure 1. Preparation steps of TiO2 solution, completion of TiO2 coating on stainless steel sheet substrates at different annealing temperatures, drug loading into the injectors by dip-coating.
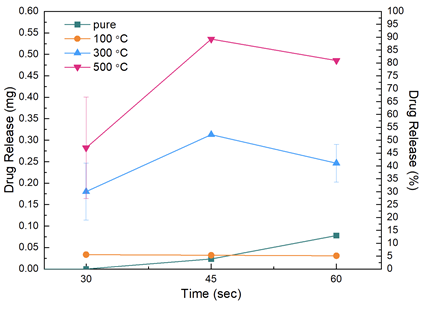
Figure 2. Drug release results were given as mg vs 30, 45 and 60 seconds for non-coated injectors and injectors that calcinated at 100 °C, 300 °C and 500 °C. The release studies were carried out at pH 7.4 buffer solution.
Sensor on non-woven
This study focuses on the fabrication of a novel, flexible and disposable textile based biosensing platform by the use of an absorbent microfibrous nonwoven substrate as the base material. This platform was fabricated via photolithography technique. Physical barriers were designed using a hydrophobic photo-resist polymer which defined the liquid penetration pathways on the fabric surface. The potential of the system was tested by constructing an enzyme biosensor based on colorimetric detection of lactic acid and hydrogen peroxide. This bio-sensing platform may be used for the rapid detection of various kinds of analytes such as glucose, lactic acid and uric acid.
Fig. 1: (Left) Fabrication steps on non-woven substrate (Right) 5 - 10 mM : Purple; 5 mM < : Green.
Fig. 2: Visual observation of the color intensity on textile surfaces (values represent H2O2 concentrations in mM).
Vessel Engineering
In the study, PDMS surfaces were designed as geometric patterns of straight lines, cross-shapes, circular shapes or square/diamond shapes to investigate their possible effects on cell viability and proliferation. Dimensions of these structures and the distance between each structure were varied as shown in Figure 1.
The study presented a strategy to fabricate tubular scaffold structures similar to native vessel as well as efficient production of ECs from a novel source. Compared with previous methods for the fabrication of vessel-like structures, the advantage of the method was distribution of cells at a microscale resolution in 3D space and controlling of cell orientation inside the tube. The help of rolling ability of the sample can adjust the size and thickness of the tubes. The rolling time of the sample was short (within minutes) and the structure can be stable without any force. Thus, it offers an advantage for delivering of the cells inside the tube.
Plasma Nitridation
We conducted a series of experiments to study thin film mechanical properties of plasma nitrided austenitic stainless steel. The plasma nitridation was performed with a different mixture of N2 – H2 gases at temperatures from 400 to 500 oC for 15 to 240 min. It is found that nano-indentation by differential load feed (DLF) analysis provides better information on the plasma nitrided surface-only mechanical properties than micro-indentation. The modulus of elasticity is found to be independent of plasma processing conditions but it is increased by 30% after plasma nitriding. The case depth of plasma nitriding is correctly calculated by the nano-hardness measurements and it is not saturated as seen in the micro-hardness measurements.
Fig. 1: Differential load feed plots for nitrided samples with different processing durations at 450 oC and 10% N by volume in the treatment gas.
Fig. 2: Variation in elasticity with respect to nitriding time (Nitrogen ratio: 10%, Temperature: 450°C)
Designing Micro-Microbial Fuel Cell
Microbial fuel cells (MFCs), or biological fuel cells, utilize bacterias for producing electricity. The exoelectrogenic bacterias can transfer electrons produced via metabolism across the cell membrane to an external electrode; this process is called extracellular electron transfer (EET). MFC systems are using these electrons and also the H+ ions to produce an electrical potential between anode and cathode.
In the study, We are using electrically conductive PDMS/CNT/Graphene composites as electrodes, and Nafion as for the Proton Exchange Membrane (PEM). we increased the surface area of the anode by designing micro-columns that are patterned by photolithography techniques. Our micro-MFC has a total volume of 800 µl.